The Reflexive Supply Chain Stack: Sensing, Thinking, Acting
The bullwhip effect of supply chains, the thousand brains theory, locating where decisions die, and building the action layer for decisions to come alive.
Prologue: The Great Disruption
When COVID hit, the first visible cracks weren’t in hospitals or stock markets; they were in supermarket aisles. Suddenly, toilet paper disappeared. And no one really knew why. That’s how it begins: with demand-supply shifts that no one knows to model. Shifts that cannot be anticipated, yet need to be dealt with at scale.
What followed was a masterclass in system fragility. The demand curve didn’t simply move, it twisted, flipped, and raged. People stopped commuting. Offices went dark. Homes lit up. Everyone rushed to set up work-from-home stations. iPads, gaming consoles, webcams, laptops: sold out. The chip factories couldn’t keep pace. But this wasn’t just about tech.
Because chips power more than laptops, like the brake sensors, navigation, and control systems in cars, the automotive industry came to a crawl. Cars were built and ready, but couldn’t be delivered. One missing chip and the whole value chain pauses. That’s the bullwhip effect in motion: small demand spikes at the edge becoming violent cracks at the centre.
Side note | Supply chains normally plan for the bullwhip effect: predictable ripples in a well-understood system. But in an intricately interconnected industry, there are rare, systemic jolts that trigger across the entire network simultaneously: events so entangled and emergent that no model accounts for them (or can account for them), and no playbook survives first contact.
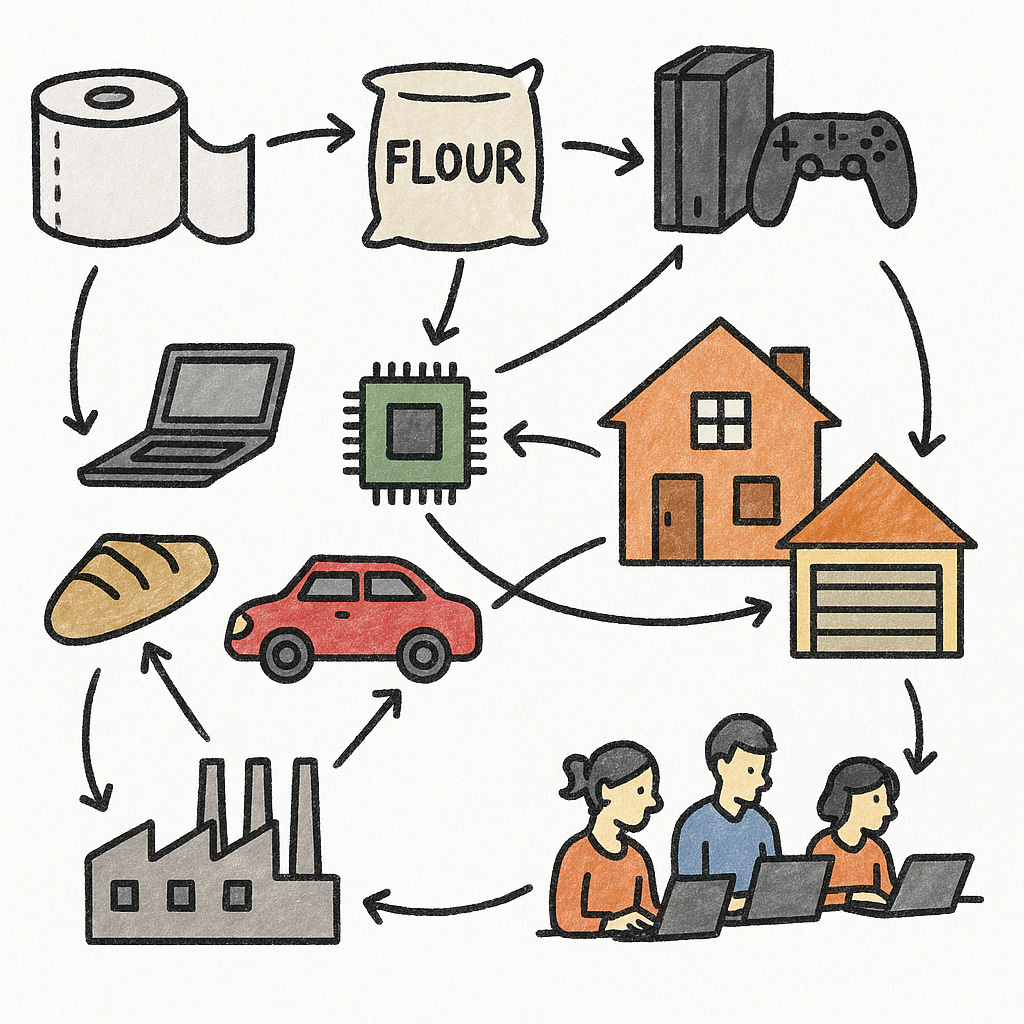
Meanwhile, something strange was also happening in the kitchens. People were making bread. Lots of it. Suddenly, flour was in short supply. Not because the wheat ran out, but because logistics couldn’t pivot fast enough to a world full of quarantine bakers.
And then came housing.
Pre-COVID, a small apartment worked fine for a family where three out of four people were out 8–10 hours a day. But when everyone had to live, work, and study within the same 2.5 rooms, tensions surfaced. Calls clashed with classes. Privacy became a luxury. So people looked for bigger homes. Demand for housing surged. Builders tried to keep up.
And just when supply seemed to catch up, garage doors ran out. Yes, garage doors. A component so mundane, it’s rarely noticed until it halts the occupancy certificate. Houses were ready. People were ready. But without garage doors, the transaction couldn’t close.
Consequently also, rental car companies’ stocks tanked. They ended up selling their cars and reducing their fleet size. As COVID ended, people worked from anywhere (staycation) more than working from offices, and rental car companies went short of cars.
The world didn’t just break. It revealed how deeply interconnected and deeply brittle our systems really are. And people began to understand: the factory isn’t just a place where goods are made. It’s the heartbeat of an invisible chain that holds modern life together.
We didn’t run out of things; we ran out of the ability to respond to people acting differently, all at once.
The Anatomy of Collapse: Understanding Fragility
In the years leading up to COVID, supply chains were temples to efficiency: fine-tuned to run lean, globally distributed, and timed down to the hour. But that same precision became their undoing. When disruption came in the form of a virus, a port jam, a policy shift. There was no slack, no backup, no room to breathe. It started with COVID, but the shocks didn’t stop with lockdowns.
We built a world on interdependence: a world where a factory pause in China or a port jam in California could be felt by a family baking bread in New Jersey or a CEO waiting on chips in Detroit. And when COVID hit, the fragility surfaced.
But then came the next wave: post-COVID churn. Each country was hit not just by viruses, but by volatility. Wars. Trade friction. Geopolitical standoffs. And all of it hit the supply chain.
One ship lodged sideways in the Suez Canal, and global trade froze as if someone had severed a critical wire. Grain shipments from Ukraine stalled as war shut down Black Sea routes. In the U.S., tariffs and a tangle of interconnected events/disruptions mean that setting up a local plant can take up to 3 years for approvals and nearly a decade to become operational. By then, your demand signal is obsolete. And when tariffs hit Mexico or Canada, vehicle pricing becomes a moving target, too unstable to plan.
Suddenly, every manufacturer, every logistics provider, every buyer and planner was forced into the same realisation: the old playbooks wouldn’t cut it.
They needed alternatives. They needed speed. They needed to act, not just analyse. Because insights without action don’t make operations better.
And this is where supply chain resilience is a requirement. Not just resilience as recovery, but resilience as adaptability. The ability to pivot in real time. To reroute, replan, rebuild on signal.
And tech and data are far from being the protagonists; they’re the enablers. The new nervous system. But a nervous system means nothing if the limbs don’t move.
And this is the shift: from data visibility to data responsiveness. From tracking to reacting. From insights to ops-level decisions that shape daily life, whether it’s getting food on shelves, cars on roads, or homes certified and livable.
That’s the anatomy of collapse. But also, the anatomy of resilience.
The New Muscle: Data-Driven Operations
When people talk about “data-driven decisions,” it often sounds like strategy decks and future bets. But the real power of data shows up in operations: in the practical, high-pressure calls teams have to make every single day.
Take the warehouse floor. You’re staring at incoming shipments, outbound delays, workers stretched thin, and pallets waiting outside in the heat, not because there’s no space, but because no one saw the imbalance coming.
Now imagine a system where that visibility exists upstream: a unified data plane pulling signals from ERP systems, warehouse software, labour schedules, weather feeds, IoT sensors; all stitched together to give you one simple truth: a particular warehouse is approaching a stockout, or another is nearing overload.
And from that truth, a decision. Reroute inbound stock from an overfilled node to one with slack. Accept a slightly lower fulfilment ratio to avoid gridlock. Keep goods moving, floors clear, and people focused on the right tasks at the right time.
This isn’t analytics for reporting’s sake. This is data activated through infrastructure and design: decision apps, operational dashboards, and real-time alerting. All of it built to translate signal into action. In an environment where resilience is a daily negotiation, this is the new muscle organisations are learning to flex.
AI as Thousand Brains, Not a Brain
"A Thousand Brains" proposes that intelligence arises from thousands of parallel models in the brain: each learning its own version of the world through movement and sensation, then voting together to form perception and understanding.
AI, when done right, isn’t some giant thinking machine sitting on top of your business telling you what to do. It’s more like a nerve reflex: fast, localised, purpose-built to classify situations and suggest next steps before you’ve had a chance to blink.
It’s not asking "what happened last quarter," it’s saying "here’s what’s happening right now, and here’s what you should do."
Take something as real as sensor data from refrigerated trucks. You’ve got five thermometers inside a moving truck, pinging data every 2-6 minutes. You know the route, the contents, the load configuration, the ideal temperature bands for different zones, and which parts of the truck tend to warm up faster, say, the rear left corner, always taking the sun.
Now the truck is delayed, and there's a risk of spoilage for items closest to the edge. If you have that insight in real-time, you’re not just flagging the problem, you’re deciding how to unload: maybe you flip from FIFO to LIFO so those warmer items hit the shelves first.
A Thousand Brains Disconnected from the Body
A Thousand Brains proposes a new theory of intelligence where each cortical column in the neocortex acts as an independent model of the world, learning through movement and sensation. These models work in parallel, constantly voting and updating based on new inputs, enabling rapid, localised decisions (causing the reflex to move your hand when it touches a hotpot).
This architecture naturally supports intelligence at the edge: decentralised, context-aware, and capable of acting without waiting for top-down instructions, just like how individual sensors or systems in a distributed network might adapt in real-time.
Recognising a pattern, mapping it to a type, and triggering an appropriate action. And it’s not just logistics. Imagine a sales rep standing at a retailer’s storefront. Instead of toggling dashboards or combing through reports, they’re nudged automatically to push a specific product line based on retailer history, shelf turnover, and the upcoming festival calendar.
But what if the intelligence is disconnected from the edge? The hand taking the call burns.
The Inflexion Point: Where Decision Dies
Everything we discussed above is well and good. Truck coming and going, all the nuances unfolding, and based on that, ideally, you’re making the decision so quickly.
The problem is, the decision is not being taken.
Since whoever is implementing AI now, what they are doing is seeing the complete data, learning, training, deploying algorithms, and after deploying, there would be some understanding, and they will get some recommendations from that. Then, who will implement and who will not is a spaghetti zone.
This is the gap in most AI deployments today: the delay between insight and action. You don’t need more dashboards. You need AI embedded directly into workflows so that the moment a decision needs to be made, the system reflexively suggests the move. Not in theory. In the moment. Where it counts.
The New Stack of Supply Chain Resilience: Bridging the Disconnect
Most organisations today have three systems running in parallel, but rarely in sync. One is for analytics (analytical systems), where teams look back at what happened. Another is for AI/ML (decision/prediction systems), where models try to guess what might happen. And the third is the operational systems where the real world actually unfolds, minute by minute.
The problem? These systems don’t talk to each other. The insight hardly ever reaches the operator. The recommendation never makes it into the operational workflow. The decision never translates into action.
A unified data platform closes that loop. It brings these systems together into a unified flow, not by replacing them, but by weaving them into a fabric where information moves frictionlessly from sensing, to thinking, to acting.
What emerges is a real Action Layer: one that shows up in the moment, inside the actual tools people use, at the exact points where decisions need to be made.
No swivel-chair between dashboards and execution. No handoff delays. No insight without ownership. Just data that moves and moves people with it.
The Future: Autonomy with Accountability
We’re headed toward a world where supply chains won’t just react but adapt. Pipelines that sense failure modes and route around them. Planning systems that shift from “what happened” to “what’s likely next.” Decisions are made faster, sometimes made automatically.
But autonomy is never the full story.
Because as we hand off more control to systems, we also have to get sharper about the lines of accountability. Who’s responsible when an AI makes the wrong call? How do we ensure transparency instead of just accuracy in machine-led decisions? And how do we make sure our drive for efficiency doesn’t override our responsibility to the environment, or to the people these systems are meant to serve?
That’s the balance. Building for autonomy but never at the cost of judgment, ethics, or long-term resilience.
MD101 Support ☎️
If you have any queries about the piece, feel free to connect with the author(s). Or feel free to connect with the MD101 team directly at community@moderndata101.com 🧡
Author Connect
Find me on LinkedIn 💬